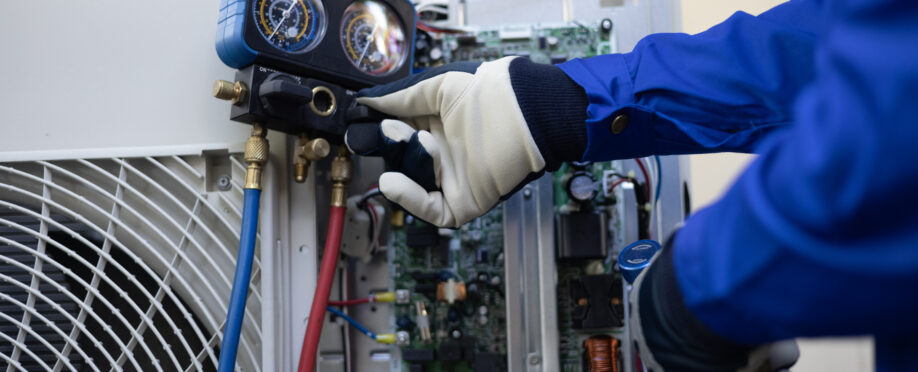
While critical, asset lifecycle management is often a poorly understood and planned component of retail facilities management.
Over 80% of companies experience unplanned downtime of critical assets at least once every three years, with most suffering two or more incidents. And retail operations — due to the high reliance on technology, equipment, and infrastructure — are even more prone to disruptions. When assets like refrigerated cases or ovens operate suboptimally or fail entirely, the impact on sales, profits, and customer loyalty quickly adds up.
With a properly structured asset lifecycle program, retail facilities leaders can maximize operational efficiency while minimizing expenses, ultimately helping them reach facilities management goals.
Managing assets comes with inevitable costs, but as Erick Brown, Director of Energy for City, notes, “You’re going to pay for it one way or the other.” Whether through ongoing maintenance or eventual replacement, facilities leaders must account for asset upkeep expenses in some form.
In this article, we’ll demystify asset lifecycle management for retailers and cover:
- What asset lifecycle management is
- The phases of an asset’s lifecycle
- Vital steps for an effective asset lifecycle program
- How facilities leaders can balance costs and benefits through data-driven decision making
Optimizing your asset lifecycle ultimately comes down to taking a proactive approach. Read on as industry experts weigh in on how retailers can master asset lifecycle management -– and boost their bottom line.
What Is Asset Lifecycle Management?
Asset lifecycle management refers to the strategic coordination of activities related to acquiring, operating, maintaining, upgrading, and disposing physical assets, such as equipment and facilities, in order to optimize productivity and expenses throughout the usable lifetime.
In essence, it’s a proactive, data-driven approach to balancing capital expenses (CapEx, which are expenditures for acquiring/upgrading physical assets) with operating expenses (OpEx, which are costs for operating, maintaining, and repairing assets) — all while maximizing efficiency and reliability.
What are the 5 phases of an asset lifecycle?
The lifecycle of a physical asset comprises five key phases:
- Acquisition: The procurement of the asset — whether through buying, leasing, or construction.
- Installation: Delivery, installation, testing, and commissioning of the asset to prepare it for use.
- Operation and maintenance: The asset’s period of regular functionality and productivity within the facilities environment. Preventive maintenance is carried out to maximize performance and lifespan.
- Upgrades and retrofits: Enhancements and updates to improve the asset’s safety, efficiency, or capabilities.
- Retirement and renewal: Decommissioning and removal of the asset at the end of its usable life. Data on reliability and cost history informs decisions on whether to replace or renew the asset.
Optimizing each phase to extract maximum value depends on aligning CapEx and OpEx through data insights, which is the foundation of sound asset lifecycle management.
Steps for Effective Asset Lifecycle Management
Implementing an asset lifecycle management program requires strategic coordination across an organization. Flexible frameworks are essential for catering to unique business needs, while adhering to the core best practices outlined below enables retailers to achieve success.
1. Commit to a proactive approach
The first step is a vital one — ensuring a commitment to a proactive asset management strategy focused on lifecycle optimization.
As Cristee Monahan, VP of Central Operations for City, notes, “The degree of proactivity will differ from organization to organization, but without alignment, even the most carefully planned lifecycle strategies are unlikely to succeed.”
The degree of proactivity will differ from organization to organization, but without alignment, even the most carefully planned lifecycle strategies are unlikely to succeed.Cristee Monahan, VP of Central Operations for City
While transitioning from reactive practices requires upfront investment, this approach — a key facilities management best practice — saves significantly on maintenance and replacement costs over time.
Cristee advises defining an asset management policy that’s aligned to business goals, such as sustainability or customer experience. Once that’s taken care of, you can garner support across departments to enable the policy’s execution.
2. Define asset quality expectations
Once leadership backs a set policy, facilities managers must decide on suitable asset performance and corresponding lifespans and define standards for asset quality accordingly. Some deterioration is expected over time, but performance shouldn’t impact operations
“Facilities managers should have the flexibility to adapt asset lifecycle planning to suit different business strategies or budget scenarios,” Cristee explains. This involves clearly defining asset performance benchmarks and ideal replacement cycles to inform maintenance workflows and capital allocation while remaining adaptable based on changing business needs.
Cristee adds, “We can build it to where you never have a fryer older than three years old. Or if capital is limited, we can plan for more temporary fixes. It all depends on the priorities.”
Cataloguing all equipment assets is critical. While doing so, detail specifications such as expected useful life, warranty periods, and ideal replacement cycle. This knowledge will guide both maintenance workflow and capital planning.
3. Leverage data for decisions
An asset lifecycle program relies heavily on data insights to drive strategic decisions on maintenance activities and equipment replacements and upgrades. Leveraging a ranking system like City’s RAG (Red, Amber, Green) status provides asset quality transparency.
As Cristee explains, “With RAG status, we use colors to rank asset quality — with red denoting assets in poor condition, amber meaning fair, and green indicating assets in good shape.”
The above is just an example — facilities management teams can define their own criteria and create a coding system tailored to their needs.
Collect detailed lifecycle cost data on expenses like acquisition, maintenance parts and labor, downtime losses, and disposal and renewal fees. Tracking reliability metrics will help estimate both the probability and impact of failures.
4. Consider hidden costs
“When evaluating asset investments, it’s important to consider not just the upfront costs, but also the hidden expenses that can accumulate over time,” Erick says. “Ask yourself: How does the downtime of that piece of equipment affect your operations?”
When making asset investment decisions, it will be found that the full financial impact extends beyond upfront capital expenses and maintenance costs.
Hidden costs over an asset’s lifetime can include:
- Revenue losses from equipment downtime, affecting sales and resulting in product loss
- Customer dissatisfaction that could lead to loss of business if retail stores feel dated or unreliable
- Employee frustration and potential turnover due to chronically faulty assets
- Compliance and regulatory risks, especially in strictly regulated states like California
While challenging to quantify, these indirect expenses can be significant over an asset’s lifetime and can help justify proactive investments. Keep them in mind during lifecycle cost-benefit analyses to make more informed decisions.
5. Utilize a robust asset management system
Implementing the right underlying asset management system, such as City’s integrated IoT platform, is crucial for executing asset lifecycle management successfully. This facilitates collecting and organizing the data needed for informed asset decision-making.
“A robust management system is mission critical for understanding what’s happening across assets in real time and planning strategic moves that maximize lifecycles.” Cristee says
A robust management system is mission critical for understanding what’s happening across assets in real time and planning strategic moves that maximize lifecycles.Cristee Monahan, VP of Central Operations for City
Key features should include:
- Predictive maintenance capabilities for real-time equipment monitoring and issue detection
- Mobile accessibility so field technicians can easily view asset histories for improved troubleshooting
- Feedback collection mechanism to drive continuous program improvements
These system features allow for the easy capture and analysis of critical data that enables facilities to optimize operating expenses throughout asset lifecycles and extract the fullest potential from their facilities investments.
Get Ahead of the Asset Lifecycle
Implementing a structured asset lifecycle management program pays dividends across retail stores through optimized equipment utilization, informed capital allocation, controlled operating expenses, and strengthened risk management.
While moving away from reactive approaches requires commitment across an organization, the Total Cost of Ownership reductions and performance improvements quickly justify the effort. And with increasingly stringent sustainability expectations on retailers, lifecycle thinking enables companies to meet compliance needs in a cost-effective manner.
As part of our industry-disruptive, data-driven facilities management system, City partners with grocery stores, convenience stores, and other retailers to implement customized asset lifecycle initiatives for maximum efficiency and cost savings. Our integrated IoT platform provides intelligent insights to optimize the asset journey from procurement to disposition. Learn more about our integrated facilities management services.