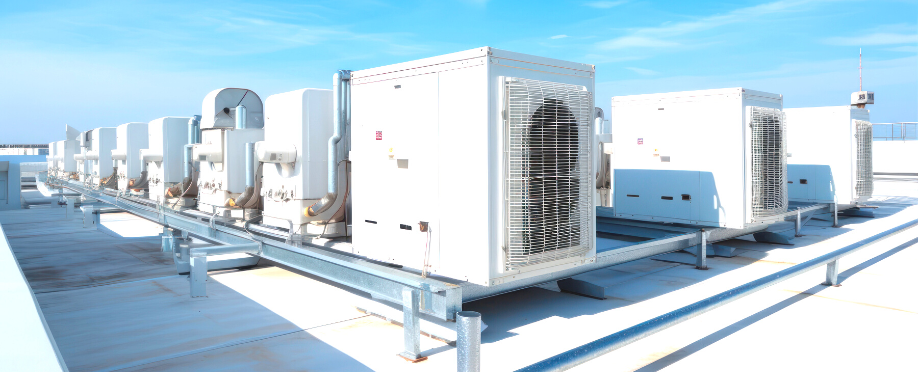
If you’re looking to save on energy costs, extend the life of building MEP (mechanical, electrical and plumbing which includes HVAC, refrigeration, and control system) assets, and reduce greenhouse gas emissions, commissioning and its sibling, recommissioning, are two of the lowest-hanging fruits available to facilities management teams.
Below we cover some key things you need to know about performing MEP commissioning and recommissioning in commercial buildings, and we offer some tips to ensure your results are as successful as possible.
What Is Commissioning in Construction?
Commissioning vs. Recommissioning
What Is Continuous Commissioning?
7 Tips for a Successful Commissioning and Recommissioning Program
Types of Commissioning
Commissioning is a process that ensures that all building MEP systems and components are thoroughly tested, verified, and optimized to meet design specifications and operational requirements, ultimately guaranteeing the functionality, efficiency, safety, and — increasingly these days — the sustainability of a facility. Today we’ll be covering the three main types of commissioning:
- New construction commissioning (Cx)
- Recommissioning (ReCx)
- Continuous commissioning
What Is Commissioning in Construction?
New construction commissioning (“Cx”) is a systematic process to ensure that a newly constructed building or newly constructed building MEP systems and components are designed, installed, tested, operated, and maintained according to the owner’s operational needs, performance expectations, design documents, and construction contracts.
“Cx isn’t about doing what you think is best or making systems more energy-efficient,” says Tom Mathews, a mechanical engineer and industry expert with nearly four decades of experience in the food retailing and distribution industries. “It’s aimed at making sure that for new or remodel construction projects, the owner receives the equipment and building systems they paid for, exactly as designed for them.”
Tom adds, “In a new building’s life, the worst year of operation is very often the first year because minor — and sometimes major — mistakes made during the construction process don’t show up until the building is in use, and then there’s hell to pay when those mistakes start to cause mischief, such as water on floors, spaces that are too hot or too cold, high humidity and the mold that comes with it, and other issues. New building Cx is intended to reduce these problems and make that first year a better experience for the building, its occupants, and the staff who operate and maintain the building.”
In new construction commissioning, there are typically six steps:
- Pre-Design Phase: This phase involves setting the foundation for Cx by establishing project goals, scope, roles, and responsibilities, and developing a Cx plan with the specific equipment and building systems that are being commissioned and to which specifications.
- Design Phase: During this phase, the design documents are reviewed to ensure they align with the project requirements, performance goals, and intended functionality.
- Construction Phase: In this phase, the actual construction takes place, and the Cx team monitors the installation of systems and equipment to ensure they adhere to design specifications.
- Testing and Documentation Phase: Functional tests are conducted to verify that systems and components operate correctly. Documentation of equipment and systems, including manuals and procedures, is also compiled in a report for the owner.
- Training and Owner Acceptance Phase: The operations team receives training on how to effectively operate and maintain the systems. The owner reviews the Cx documentation and confirms their acceptance of the project.
- Post-Occupancy and Warranty Phase: After the building is occupied, the Cx team continues to monitor and address any operational issues that arise, ensuring the systems perform as intended. Any warranty-related matters are also addressed during this phase.
These phases collectively ensure that the new construction project is thoroughly commissioned, resulting in a functional, energy efficient, reliable, and sustainable facility.
“While there are of course technical aspects, Cx is also a highly administrative process,” Tom says. “There’s a lot of documentation involved as well as other administrative tasks like compiling data from tests and inspections, preparing reports, and completing sign-off requirements. CxAs (Cx agents) are responsible for seeing that the building is built correctly and completely in all respects. That requires more than just inspections and tests.”
Commissioning vs. Recommissioning
Recommissioning, or ReCx (sometimes ”RCx” or “existing building Cx” or other names), is similar to Cx in that it involves inspecting and testing building MEP systems and equipment, but it goes beyond identifying and carefully documenting issues and deficiencies and their resolution to include actually making repairs, adjustments, and minor upgrades.
ReCx is usually applied to existing, older buildings, not new or newer buildings, unless a newer facility has gotten off to a poor start and is plagued with comfort or other operating issues, excessive energy usage, or frequent system or equipment failures. ReCx has the following goals:
- Making a piece of equipment, building system, or building function more optimally or in a more energy-efficient way
- Extending the life of the MEP asset or equipment and the building
- Reducing GHG emissions (a newer ReCx scope element)
Often, this means adjusting MEP systems to operate in a way that reflects updated standards, techniques, and technologies — not the original design documents, specifications, and control schemes for the building MEP systems.
Whereas the commissioning process involves inspecting and testing a brand new MEP system or piece of equipment or arranging for the responsible parties to make corrections, repairs, and adjustments to meet the building design requirements and specifications, recommissioning is always performed in an existing building on an existing MEP system or piece of equipment.
ReCx falls into two categories:
- Owner-sponsored ReCx
- ReCx sponsored by a utility, state, or energy-efficiency organization, which may contribute significantly to the cost of the program
Owner-sponsored ReCx is usually focused on reducing energy expenses during periods of rising electricity and/or heating fuel costs or getting building MEP system operating issues such as high building humidity under control. Owners are often reluctant to roll out large, multisite ReCx programs because the expense of ReCx normally cannot be capitalized and must be expensed during the current fiscal year. When energy prices are high and rising higher, simple paybacks of less than a year can be achieved, and ReCx helps rather than hurts financial results in the current year.
Recommissioning sponsored by third parties usually include incentive payments, which can help offset ReCx expenses and reduce finance department resistance and approval barriers. Utility and governmental interest in energy efficiency and GHG emission reductions and the decline in low-hanging-fruit energy efficiency measures such as LED lighting retrofits means these third parties are turning more and more to recommissioning to deliver improved building energy efficiency and energy usage and GHG emission reductions. This is spurring renewed interest in ReCx.
The ReCx process is substantially less administrative compared to the Cx process and comprises the following steps:
- Assessment: Gather data remotely from building and equipment control systems and manuals, review original design documents, and assess systems and equipment to identify possible issue/deficiency areas.
- Testing and Analysis: Test systems, analyze results, and find performance deviations and opportunities for performance improvements.
- Recommendations: Develop actionable solutions and execute or collaborate on implementation.
- Training and Communication: Train staff, address questions, and encourage feedback.
- Validation and Documentation: Verify improvements, document actions, and prepare a summary report.
But the process doesn’t stop there — at least for Tom. “For best results, recommissioning should be partnered with continuous commissioning to ensure all improvements and benefits are sustained and the facilities team detects any new issues or opportunities for improvement.”
This brings us to the third type of commissioning …
What Is Continuous Commissioning?
With continuous commissioning, smart engineers and technicians or smart algorithms, or both, monitor and optimize building systems in real-time, ensuring energy efficiency and operational performance.
Continuous commissioning is generally a process done remotely or partially remotely with assistance by personnel at the building or facility. It involves remotely collecting data from a site with electronic or computerized facility control systems, which may be known as any of the following:
- BCS: Building control systems.
- BAS: Building automation system
- BMS: Building management system
- FMS: Facilities management systems
These systems operate continuously, gathering data either through manual or automated processes. This data undergoes analysis, performed either manually by human experts or automatically using software. The primary aim is to identify any issues or opportunities related to MEP system and equipment energy usage or operation.
Continuous commissioning agents then determine the necessary actions, which may include remote adjustments, such as calibration or modifications to control systems. In some cases, on-site service providers may need to be dispatched if remote interventions are not possible or successful.
For example, a smart algorithm might detect that an undersized or aging building HVAC system struggles to maintain indoor temperatures in very hot outdoor temperature conditions unless all the air conditioning system compressors get a “head start” before outdoor temperatures reach 80 degrees. Commissioning agents might adjust the control program accordingly so that when the outdoor temperature is approaching 80 degrees, all the HVAC compressors turn on, allowing the unit to successfully maintain indoor temperatures at comfortable levels and ride through the outdoor temperature spike.
Continuous Commissioning vs. Continuous Monitoring
Continuous commissioning and continuous monitoring could be said to be twin brothers; however, continuous monitoring is different in that the process often starts remotely and continues remotely without the dispatch of technicians to the site.
Tom recommends doing ReCx on site before starting continuous commissioning because there are certain issues that can’t be detected remotely. He explains, “For example, you wouldn’t be able to see that the outside temperature sensor has accidentally been installed where the sun shines on it from ten in the morning to two in the afternoon, making the outdoor temperature appear much higher than the actual air temperature.” Doing ReCx before starting continuous commissioning allows these kinds of issues to be cleaned up, improving the results of continuous commissioning.
Continuous commissioning is closely related to condition-based maintenance, which involves monitoring the same data, but the actions are targeted at determining the necessary maintenance or repair activity repairs, not necessarily optimizing building performance and energy efficiency.
“Eventually everything will be continuously commissioned in order to ensure operating efficiency and minimal GHG emissions,” Tom says. “The cars we drive today are a good example. The computer in the car monitors all the key vehicle systems. When it sees a defect such as high fuel usage, incorrect exhaust gas levels, or other indication of poor performance, it sometimes makes automatic adjustments, or it alerts the user that the car needs to be serviced by a mechanic and then tells the mechanic what the problem is and how to correct it. This is where maintenance and repair of the built environment is inevitably heading with the current and likely future scarcity of trained service technicians, the increasingly complex building MEP systems, and the increasing need for energy and GHG emission reductions, backed up by high energy prices and increasing governmental regulation and emissions penalties.”
Eventually everything will be continuously commissioned in order to ensure operating efficiency and minimal GHG emissions.Tom Mathews, SVP of Sustainability at CBES
Seven Tips for a Successful Commissioning or Recommissioning Program
1. For ReCx, focus on the most important equipment or systems
The importance of the equipment or system with respect to successful operation of the facility determines what you’re going to focus on. With ReCx in food retail facilities, for example, keeping things cold is mission critical and the equipment meeting this mission requirement uses a lot of energy and accounts for a large fraction of building GHG emissions. Thus, commercial refrigeration units would get more attention and a deeper level of Cx or ReCx.
“Not everything has the same value. Look for items that will waste energy 40 percent of the time, cause GHC emissions 60 percent of the time, or interfere with operations a lot of the time,” Tom says. “For instance, you don’t waste your time inspecting and repairing strip curtains installed on loading docks only to have them cut down after they interfere with the work of receivers. This issue is best handled outside of ReCx via capital spend on loading dock improvements and dock seals, which are effective and permanent.”
With Cx, on the other hand, everything within the building design documents and construction contracts gets commissioned (inspected, tested, and corrected where necessary) regardless of apparent or current importance.
2. Understand the difference between commissioning and recommissioning
Cx and ReCx are similar in that they both involve the evaluation, testing, and optimization of building systems and equipment to ensure they operate efficiently and effectively. But unlike Cx, ReCx is less of an administrative process focused on careful documentation.
“The design documents and specifications are the reference Bible for Cx. One commissions against those, not against personal preference, or belief, or even what is considered current best industry practice by most,” Tom says.
This isn’t the case for ReCx, however. Agreement on any changes made to MEP systems and equipment operation, configuration, or control are based on the ReCx agents’ knowledge and expertise, current best practices, and other reference points. The original building MEP design documents and specifications are still relevant but not, according to Tom, “absolute.”
“With new construction Cx, all knowledgeable Cx agents are doing the same thing, guided by standard documents and procedures, although you’ll see some differences in outcome based on the agents’ communication skills,” Tom says. “On the other hand, ReCx is like being thrown directly into battle. ReCx needs to perform a number of investigative procedures. There’s still a level of bureaucracy, but it’s about getting results. Recommissioning agents download available building MEP history from the building control systems to see how the building has been operating, they inspect, they test, they adjust, they repair or get repairs made — they get results. Careful documentation is still of course necessary, but it is not the centerpiece of the ReCx effort — the street fight is.”
3. Ensure thorough, meticulous design specifications for new construction Cx
It’s important to keep in mind that with new construction commissioning, the end product can only be as successful as the availability of comprehensive high-quality specification and design documents for that project.
Tom offers an example: “It’s pretty common for a rooftop HVAC unit to lack screws fixing it to the roof curb. As securing the unit is extra work if it isn’t called for in the installation specifications, it often goes undone. In the south, after major storms, it’s easy to see which ones were screwed down and which weren’t — those that are found in the parking lot weren’t!” Ensuring that such best practices are included or referenced in the design specification documents can help ensure that such deficiencies, which may have potentially serious risks, are checked for and resolved.
4. Understand the importance of continuous commissioning
It’s been shown that even in food retail chains with well-managed facility management departments and processes, energy can drift by 2 percent year over year without ongoing central remote monitoring of the building MEP systems.
By continuously monitoring the operation of a facility’s energy-consuming systems and equipment in close-to-real-time after ReCx (and after Cx), facilities managers can not only minimize electricity and refrigerant usage but also respond quickly and effectively to any equipment issues before they become emergencies. This leads to reduced maintenance expense, equipment failures, poor store conditions and other consequences.
This is why at CBES, ReCx is performed by ReCx professionals in conjunction with a remote commissioning team, who provide continuous commissioning after the project is completed.
“We simply won’t take on a ReCx project unless the customer agrees to two years of continuous commissioning because that’s the minimum time it takes to change the behavior of the building operators and service providers,” Tom explains.
5. Make sure you have a dedicated ReCx team
One of the most common problems owners run into with ReCx is a team that isn’t committed for the entire duration of the ReCx project.
“Whether they’re electricians or R/HVAC technicians, they may have other responsibilities and can get pulled off for service calls during the two to four days that it takes to complete the recommissioning,” Tom explains. “At CBES, one of our requirements of the technicians who participate in recommissioning is that they remain dedicated to each project until it’s complete.”
6. Facilitate effective communication and collaboration
With Cx or ReCx teams, granting access to all passwords, programs, and set points is vital. With ReCx in particular, the owner should stay in close communication with all the facilities managers, service providers, and other interested parties to ensure there are no misunderstandings or errors that could pose an issue for the store or ReCx agents doing the work.
Such collaboration requires kick-off meetings, review meetings, and tight management and discipline to get the desired result. Make sure to choose a ReCx provider that is committed to staying in communication and working with others.
7. Use cutting-edge software
When vetting providers, make sure to ask them what software tools they use. “For either Cx or ReCx, if the agents show up with a clipboard or an iPad with an Excel spreadsheet, send them packing,” Tom says. “You want to see them using software that allows them to quickly and expertly acquire the information needed to successfully document the condition of the equipment, system, or building with many photographs and complete, well-composed, and consistent issue descriptions, which are the best evidence and most informative source of information. You’ve got to have the right tools.”
Sustainable Energy Solutions for the Future of Retail
In today’s global environment, it’s more important than ever for food retailers and other commercial facilities to do their part in reducing energy consumption and greenhouse gas emissions. By following the tips above for commissioning and recommissioning projects, FM leaders can have a significant impact on their facilities as well as on the planet.