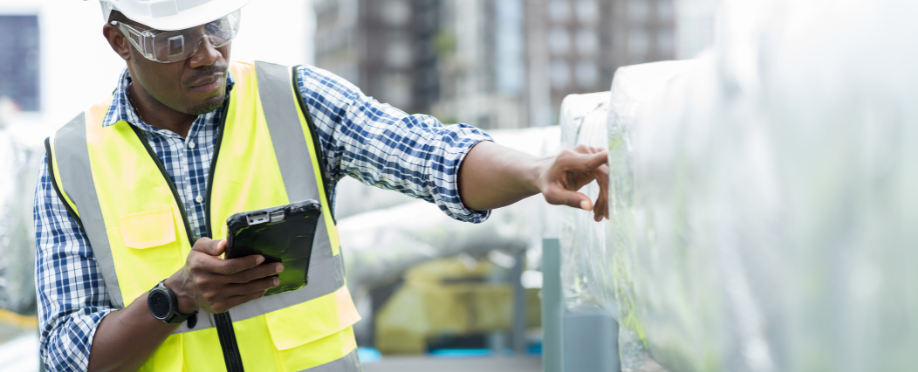
Retailers know all too well the costly disruptions that unexpected equipment failures can wreak: perishable stock spoiled, health codes breached, and customers left frustrated. In a competitive market where customer loyalty is key, avoiding these operational setbacks is essential. Predictive maintenance gives retailers the foresight to anticipate issues, helping them keep operations running smoothly and profitably.
Put simply, predictive maintenance uses data and technology to detect issues before catastrophic failure occurs, allowing facilities management teams to schedule repairs at opportune times. According to the US Department of Energy, implementing predictive maintenance programs in an industrial setting can yield impressive results — including a 10x return on investment, 25–30% reduction in maintenance costs, 70–75% elimination of breakdowns, 35–45% reduction in downtime, and a 20–25% increase in production.
For food retailers, this can mean fewer refrigeration breakdowns, less spoiled inventory, and improved operational efficiency.
Here’s what facilities managers need to know about getting started with predictive maintenance.
What Is Predictive Maintenance?
Predictive maintenance refers to maintenance strategies that use data analytics, specialized tests, sensor technology, and artificial intelligence (AI) to predict when anomalies or equipment failures are likely to occur. This allows issues to be addressed before they cause downtime.
What is the difference between predictive and preventive maintenance?
While preventive maintenance involves general upkeep to maintain assets, predictive maintenance uses technology and data to pinpoint emerging issues before they become failures. Preventive maintenance follows a schedule, while predictive maintenance is conditioned-based, happening only when red flags are detected.
Key benefits of predictive maintenance
There are several major advantages predictive maintenance offers facilities managers:
- Operational benefits: By detecting equipment issues before actual failures and providing clear details on the repairs needed, predictive maintenance can significantly increase uptime.
- Financial benefits: Predictive maintenance can lead to significant savings by reducing technician overtime costs, extending the life of expensive equipment, and avoiding shrink from lost product when refrigeration fails.
- Labor benefits: By enabling maintenance to be scheduled proactively, predictive maintenance can eliminate most emergency after-hours and maintenance calls, improving work-life balance and retention for field technicians. The technology is also easy to use and learn, provides detailed instructions for repair work, and can assist with technician training.
The benefits above apply broadly to all types of predictive maintenance technology, including ultrasound diagnostics, remote monitoring, internet of things (IoT) sensors, AI platforms, infrared analysis, vibration analysis, and more.
“When you consider that grocery stores lose as much as over three percent of total sales each year to shrink, it’s no wonder that predictive maintenance has become one of the fastest-growing trends in food retail,” says George Campbell, Director of Technical Services at City. “Even if you reduce that by as little as 10%, the cost savings can be enormous.”
When you consider that grocery stores lose as much as over three percent of total sales each year to shrink, even if you reduce that by as little as 10%, the cost savings can be enormous.George Campbell, Director of Technical Services at City
Types of Predictive Maintenance
While it’s been around for decades, predictive maintenance has skyrocketed in recent years, as cutting-edge technologies like AI and IoT unlock powerful new capabilities that were once unimaginable.
Here are the three main types of predictive maintenance retail facilities managers are leveraging:
1. Data-driven predictive maintenance
This approach harnesses historical data, asset trends, predictive analytics, and AI to pinpoint probable failures before they occur. Advanced algorithms examine past performance data and breakdowns to determine when similar issues are likely to surface.
Predictive analytics software enables predictive maintenance by leveraging both historical and real-time data to uncover patterns, allowing for the anticipation of failure risks before they cause shutdowns. Such platforms, especially ones with AI-powered capabilities, are becoming increasingly prevalent.
2. Condition-based monitoring
Real-time condition tracking leverages IoT sensors to constantly feed data on parameters such as equipment vibration, operating temperature, noise emission, and other telling proxy signals. If measurements drift out of defined acceptable bands, proactive alerts trigger, allowing issues to be addressed before outright failure happens.
Take temperature monitoring for instance: It enables constant oversight of fridge and freezer conditions to enable cold chain continuity. Alerts allow teams to quickly handle temperature fluctuations before spoilage results.
Some IoT platforms enable monitoring of multiple systems. For example, City’s SPARK+ continuous monitoring platform oversees refrigeration, HVAC, and other systems in real-time 24/7 to enable immediate anomaly detection. SPARK+ precisely tracks critical temperature and energy data and notifies predictive diagnostics teams to deviations that could signify impending equipment failures.
3. Remote sensing and diagnostic technologies
Remote diagnostic techniques access equipment data in real time, often from off-site locations. These technologies, ranging from IoT sensors to machine learning, typically couple predictive analytics to uncover emerging risks like leaks, wear, and energy inefficiencies before they lead to breakdowns.
One example is ultrasound inspections. High-frequency soundwaves are used to detect ultrasonic sounds that signal emerging defects in mechanical systems, such as refrigerant leaks, electrical arcing, or worn-out components that could lead to equipment failure.
Predictive Maintenance Today
Predictive maintenance has moved from an emerging innovation to an essential component of a best-in-class retail facilities operation. The rapid maturation of equipment sensors, internet of things devices, remote monitoring platforms, and AI has brought predictive capabilities to the mainstream.
Despite the advantages, predictive maintenance was once relatively slow to catch on. In fact, George admits there was a time when he was reluctant to buy into the concept of predictive maintenance technology.
“My first reaction was, ‘I don’t have time for this. I’ve been doing this for 40 years. I know what’s wrong with the compressors. I don’t need some tool telling me what’s wrong,’” says Campbell, a master electrician with experience both in the field and as a leader in refrigeration and mechanical facilities maintenance.
Then George was tasked with a series of grocery store pilots to test SOUNDTech+ ultrasound technology, the City branded predictive maintenance tool powered by DST: “In our pilots, I tried to prove the tool did not work. But it surprised me every time. The tool kept proving itself.”
His initial perception of predictive maintenance technology is common among many engineers and technicians, according to research by the Manufacturers Alliance Foundation. The report, Predictive Maintenance Strategies Gain Ground, cites companies that gained significant ROI by using these technologies. However, it recommends finding a champion on the maintenance team and involving them early.
“It will involve a culture change for predictive maintenance to take off. Many companies are still in the ‘break and fix’ mentality,” said Campbell. “But at City, we want to be proactive and get ahead of problems, because we know that will ultimately save money and avoid a ton of headaches for our partners. It’s remarkable what we can do in the predictive world if we do it right. People just don’t believe it until they see it.”
Get Ahead of the Predictive Curve
With equipment downtime costing retailers up to millions per year, predictive maintenance technology represents one of the most pivotal investments facilities managers can make today. As predictive offerings extend insights across HVAC systems, compactors, fire pumps, and beyond, the potential to optimize maintenance resource allocation, plan ahead, capture savings, and buoy the bottom line will only increase. By tapping into predictive maintenance capabilities now, retailers can seize a tech-enabled competitive edge while propelling their operations confidently into the future.
As part of City’s industry-disruptive, data-driven delivery facilities management system for grocery stores, convenience stores, and other retailers, our Intelligence & Automation team can help implement the latest predictive maintenance best practices to boost efficiency, reliability, and intelligence across your retail facilities. Learn more about our Intelligence & Automation services.