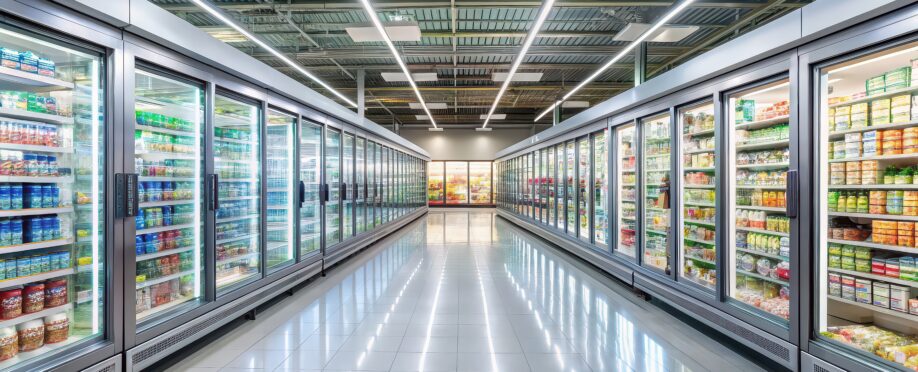
With profits tightly connected to equipment uptime, especially for retailers who rely on refrigeration systems, HVAC units, and other equipment to keep operations running smoothly, facilities management teams must make preventing equipment failures a top priority. In this article, we’ll look at what equipment downtime is, how to calculate it, the major factors that contribute to it, and most importantly, what retailers can do to minimize it through proactive maintenance strategies and technology.
By putting robust processes in place and leveraging innovations like predictive maintenance, retailers can significantly reduce the impact of equipment downtime on their bottom line. Let’s dive in to understand exactly how facilities leaders can better prevent disruptions from equipment failures.
What Is Equipment Downtime?
Equipment downtime refers to any period when a critical piece of equipment in a facility isn’t functioning or performing as expected. In retail stores, this impacts essential systems like refrigeration, HVAC, lighting, security systems, and more.
What does production equipment downtime mean?
In the context of retailers, production equipment downtime refers to instances when equipment integral to store operations experiences failure or subpar performance, directly hindering a store’s ability to function and serve customers.
How to calculate equipment downtime
Equipment downtime is calculated as a percentage indicating the amount of total downtime hours relative to hours of operation:
Downtime percentage = (Hours of Downtime / Total Hours of Operation) x 100
For example, if a refrigeration system was down for 5 hours over the span of a 100 hour work week, the downtime percentage would be 5 percent.
Major contributing factors
The major factors contributing to equipment downtime include:
- Lack of preventive maintenance
- End of equipment lifecycle or aging assets
- Improper operation
- External issues like power outages
- Software glitches
- Poor system design/integration
Impact of Equipment Downtime
When critical equipment goes down, the effects on retail stores can be far-reaching, including:
- Food spoilage and waste
- Revenue losses from disrupted operations
- Non-compliance with health codes
- Increased repair costs from secondary damage
- Lower employee productivity and satisfaction
- Poor customer experiences
According to Cristee Monahan, VP of Central Operations at City Facilities Management, “Equipment downtime, especially for refrigeration systems, directly translates to lost sales and profits. It can also negatively impact customer loyalty and brand reputation, particularly if temperature standards are compromised.”
Equipment downtime, especially for refrigeration systems, directly translates to lost sales and profits.Cristee Monahan, VP of Central Operations at City Facilities Management
How to Reduce Equipment Downtime
Retailers can get ahead of the majority of equipment downtime events through proactive maintenance strategies that detect issues early and enable rapid response.
Commit to proactive maintenance
Implementing robust preventive maintenance across all equipment and systems is fundamental to reducing downtime. As Cristee explains, “Preventive maintenance combined with the use of predictive technologies can catch the majority of equipment issues before they cause breakdowns. It requires unified commitment across the organization as well as proper planning, scheduling, and execution.”
Steps for creating a preventive maintenance program include:
- Compiling a register of equipment
- Defining maintenance tasks and frequencies
- Scheduling activities
- Tracking completion
- Analyzing performance data
- Continually optimizing approach
Adopt the right technology
Investing in facilities management technology like City’s SOUNDTech+ ultrasonic platform for predictive maintenance and proprietary SPARK+ system for continuous equipment monitoring can also significantly reduce equipment downtime.
SOUNDTech+ uses ultrasound waves to uncover mechanical issues and pinpoint failing components before total failure occurs. By enabling technicians to proactively service equipment, costly breakdowns are avoided. SPARK+ continuously monitors temperature and other performance indicators across refrigeration cases, HVAC units, and other systems. When metrics fall outside of defined ranges, alerts trigger rapid response to diagnose and address root causes.
Together, these technologies drive uptime by detecting anomalies early and enabling issues to be corrected before causing disruptions to retail operations. According to data scientists at DST, the developer behind SOUNDTech+, the solution has demonstrated up to 98 percent accuracy in predicting catastrophic refrigeration failures in field applications.
Advance technician skills
Proper training of technicians responsible for operating equipment is also key to minimizing downtime.
George Campbell, Director of Technical Services at City, emphasizes the importance of hands-on training using the actual equipment found in the retail environments technicians service: “Simulation of real-word scenarios allows technicians to hone troubleshooting and problem-solving skills, enabling faster response when issues arise.”
Simulation of real-word scenarios allows technicians to hone troubleshooting and problem-solving skills, enabling faster response when issues arise.George Campbell, Director of Technical Services at City
Plan for supply chain needs
By forging strong relationships with parts suppliers and distributors, facilities teams can ensure quick access to replacement components in the event of a breakdown. Supply chain planning helps prevent extended downtime situations due to lacking parts.
According to Cristee, “Having visibility into the supply chain and planning for contingencies is one of the most vital things a facilities management team can do to control downtime.” To achieve this, teams must ensure they have the right parts available at the right time, which requires a thorough understanding of their inventory and proactive supplier relationship management.
Promote proper equipment handling
Often, excessive equipment wear and tear can be traced back to improper usage. By training staff who regularly operate equipment on proper procedures laid out in manufacturer specifications and preventive maintenance guidelines, retailers can promote proper handling and prevent accidental damage from operational errors, thereby extending equipment lifespan.
Getting Ahead of Equipment Downtime
By taking a data-driven, proactive approach to facilities management, food retailers can stay ahead of equipment failures instead of reacting to them. Investing in robust preventive maintenance programs, predictive technologies like ultrasound sensors and real-time monitoring, proper technician training, and supply chain strategy can pay major dividends through maximized uptime.
As part of City’s data-driven facilities management approach for grocery stores, convenience stores, and other retailers, we help FM teams implement the latest tech-enabled best practices for predictive maintenance to ensure unprecedented equipment uptime. Learn more about City’s Integrated Facilities Management services.