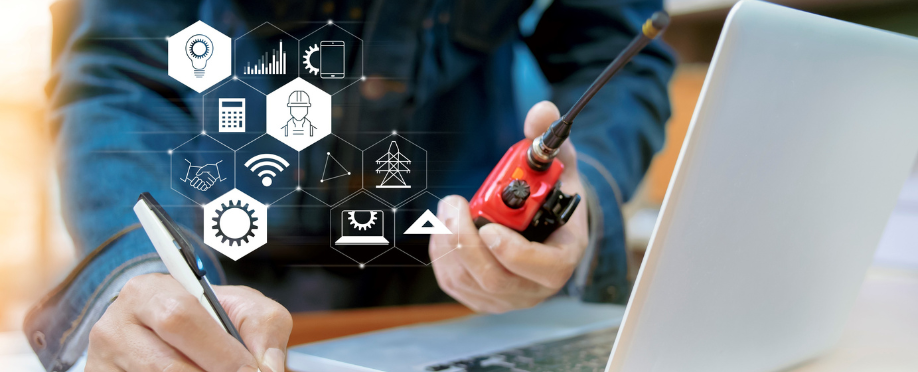
From ensuring safety to meeting the latest energy legislation — all while ensuring smooth operations and minimizing costs — retail facilities managers in the food retail space have a great deal of responsibility on their shoulders. But thanks to recent innovations in technology, FM leaders now have a wealth of tools and strategies at their disposal to ensure effectiveness.
In this article, we’ll take a look at 12 of the most vital facilities management best practices for driving success according to leading experts in the retail space.
What are facility management practices?
Good facilities management involves managing the physical spaces and assets of facilities in order to ensure the optimal functionality, safety, efficiency, and user satisfaction in alignment with an organization’s goals and activities.
Facilities management can be categorized into four pillars:
- Maintenance and repairs: Day-to-day activities, such as routine maintenance, repairs, and cleaning, required to maintain a facility’s functionality and safety
- Space management: Optimization of spaces to support a facility’s operations and enhance productivity, collaboration, and employee satisfaction
- Asset management: Managing and maximizing the performance of physical assets and equipment of a facility throughout their life cycle
- Sustainability management: Implementing environmentally responsible practices as part of the organization’s commitment to sustainability and in compliance with regulations
12 Key Facilities Management Best Practices
By implementing the following best practices, today’s facilities leaders can achieve more efficient operations with great uptime, lower costs, and greener facilities.
- Prioritize safety
- Make energy efficiency updates
- Implement sustainable refrigeration practices
- Adopt a preventive approach to maintenance
- Leverage data analytics
- Strengthen asset management
- Leverage predictive maintenance
- Implement EMS platforms
- Strengthen your supply chain
- Invest in technician training
- Prioritize emergency preparedness and response
- Adopt an integrated approach to facilities management
1. Prioritize safety
Ensuring the safety and security of facilities isn’t just a best practice — it’s the number-one priority of facilities managers, especially in the grocery industry where risks such as slips and falls, food equipment accidents, and other potential hazards are always present and can impact customers and employees alike.
Check out our grocery store safety tips for facilities leaders for a list of safety-promoting best practices.
2. Make energy efficiency updates
With both sustainability legislation and energy costs on the rise, grocers and other food retailers can’t afford — literally — not to reduce energy consumption. Effective energy efficiency updates include recommissioning existing equipment; adding variable speed control to condense fans, HVAC unit air supply fans, and compressor room exhaust fans; and repurposing waste heat as an energy source with heat reclamation.
For more energy efficiency best practices, read Food Retail Energy Efficiency Best Practices
3. Implement sustainable refrigeration practices
According to the NASRC (North American Sustainable Refrigeration Council), the average supermarket uses thousands of pounds of HFC refrigerant every year and has a leak rate of about 25 percent of the refrigerant charge. Meanwhile facilities managers are under increasing regulatory pressures to help mitigate the environmental impact of carbons.
This means gas containment and leak detection should be a priority for all food retailers in the following ways:
- Make leak detection part of every service call
- Implement refrigerant leak monitoring systems
- Commission and recommission refrigeration equipment to ensure optimal efficiency
- Use energy management systems to monitor refrigeration energy use
- Transition from high GWP (global warming potential) HFCs to low-GWP natural refrigerants such as CO2 and 2Als
For more sustainable refrigeration best practices, check out 3 Steps to Sustainable Refrigeration Management for Grocery Retailers.
4. Adopt a preventive approach to maintenance
One of the most important best practices facilities management teams can implement for increasing efficiency, reducing downtime, and saving on costs is the implementation of a preventative maintenance program. With regular inspections, cleaning, and maintenance, facilities can identify and address equipment issues before they escalate into costly failures.
Read more: 6 Elements of a Successful Preventive Maintenance Program
5. Leverage data analytics
In today’s world, data has never been so prevalent, but that doesn’t necessarily mean that it offers value.
“The value of data lies in how effectively it’s used to drive informed decisions,” says Cristee Monahan, VP for Central Operations at City. “For decades, facilities managers have had notebooks filled with data, but we never looked back at it.”
Now, however, with the advent of computers and AI, facilities management teams are able to harness data in ways previous generations would’ve never imagined possible.
“Today, data is being utilized for work orders, asset tracking, expenditure analytics, and energy consumption, just to name a few areas,” says Cristee. “Facilities managers are using such insights to prioritize maintenance efforts, streamline operations, and allocate resources efficiently.”
AI-driven predictive analytics tools, in particular, can be a powerful addition to a preventive maintenance program by helping facilities anticipate equipment failures, optimize maintenance schedules, and focus on efforts with the highest ROI. Integrating AI-powered skillset matching into work order systems can also increase first time fix rates and thus service quality.
6. Strengthen asset management
Effective asset management with meticulous tracking is the backbone of a successful facilities management program.
“Every asset has a life cycle,” says Cristee. “The goal is always to extend equipment beyond that life, and the best way to ensure that is with effective asset tracking.”
To ensure optimal performance and longevity of equipment, facilities managers should aim to track data such as:
- Maintenance frequency
- Repairs vs. preventive maintenance interventions
- Component replacements
- Life cycle costs
By monitoring data like the above, facilities can identify patterns, optimize maintenance schedules, make informed decisions about replacements, and address issues before they turn into failures.
“With proper asset management, your repairs are going to be proactive rather than reactive, so you can maintain uptime and save costs. Planned repairs are always cheaper than service calls in the middle of the night.”
7. Leverage Predictive Maintenance
While preventive maintenance helps prevent issues from occurring and extends the life of assets, predictive maintenance tools go a step further by leveraging data analytics to anticipate potential failures before they occur. Just as with preventive maintenance, such predictive tools allow facilities managers to take a proactive approach, minimizing downtime and optimizing equipment efficiency.
There are a number of different predictive maintenance technologies out there — not limited to ultrasound technology, vibration analysis infrared analysis, and predictive analytics using AI and machine learning. At City, technicians use SOUNDTech+ ultrasound technology, the City branded predictive maintenance tool powered by DST, which has a track record in the field of predicting catastrophic refrigeration rack failure before it becomes an issue — with up to 98% accuracy once the tool is programmed.
Read more: 3 Cost-Saving Benefits of Predictive Maintenance Technology
8. Implement EMS platforms
While we covered data analytics above, it’s important to call out in this era of increased sustainability regulation (not to mention, higher energy costs) the importance of utilizing EMS (energy management system) platforms paired with data tracking. By collecting and analyzing equipment performance and energy usage patterns, facilities teams can detect and handle anomalies before they turn into costly power bills while also reducing overall environmental impact.
9. Strengthen Your Supply Chain
An efficient supply chain is essential for maintaining operational continuity.
“COVID is often cited as a reason for supply shortages,” says Cristee, “but with a robust supply chain strategy any facilities management team can overcome disruptions to their supply chain.”
While direct purchasing from manufacturers is less available than before the pandemic, forging strong relationships with the high-quality regional suppliers can help ensure timely and continuous access to products.
10. Invest in technician training
With the skilled trades labor pool shrinking and the demand for more proficient technicians on the rise, investing in ongoing education has become vital for facilities management teams.
Strategies for training and developing of skilled talent include:
- Emphasizing practical application in training
- Collaborating with local communities to recruit and train young talent
- Promoting cross-training of staff
- Developing multi-skilled tradespeople
- Offering continuous technical training opportunities
The result is a happier workforce that can deliver better service quality with higher first-time rate fixes and lower repairs costs.
Read more: Facilities Management Training Tips
11. Prioritize emergency preparedness and response
In recent years, disasters have been more frequent and costly than ever, a trend that scientists are attributing to climate change.
“Though it can be hard to pinpoint whether climate change intensified a particular weather event, the trajectory is clear — hotter heat waves, drier droughts, bigger storm surges and greater snowfall,” says the Environmental Defense Fund.
“There’s no one-size-fits-all plan for weather preparation,” says Cristee, “but at City we follow a Plan, Prepare, and Protect model, which has helped our partners weather a number of a severe events without major incident.”
In the Plan phase, Cristee recommends conducting thorough location surveys, drafting preparedness and communication plans, and securing all locations based on the survey data.
Read more: Hurricane Preparedness Checklist for Facilities Managers
12. Adopt an integrated approach to facilities management
Outsourcing facilities management services now makes up a substantial part of the market, according to McKinsey, with IFM (integrated facilities management) capturing a growing share.
With IFM, a single provider uses a holistic strategy to fulfill all of a facility’s service needs on a self-perform basis. Amidst a shrinking skilled labor market, rising costs, and the increasing sophistication of today’s technologies, IFM providers can help drive cost reductions and enhanced service quality through efficiencies and the latest technology innovations.
Read more: What Is Integrated Facilities Management
The latest facilities management innovations and best practices
While the industry is rapidly changing, facilities managers are equipped with unprecedented technological advancements and innovations, allowing them to reach new heights of efficiency and effectiveness. By leveraging the best practices above, they can confidently drive a positive impact on not just their facilities but their communities and the environment as a whole.
At City, as part of our industry-disruptive, data-driven delivery system for grocery stores, convenience stores, and other retailers, we can help you implement the latest innovative best practices to improve service quality and lower costs. Learn more about our Integrated Facilities Management services.