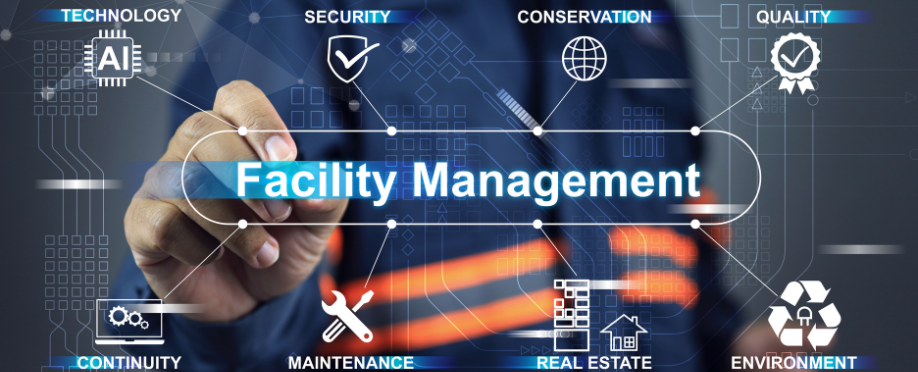
There’s no question that facilities management leaders have a lot on their plates these days. In addition to taking care of reactive maintenance to ensure maximum uptime, climate legislation is ramping up and the customer experience has never been more critical.
While accomplishing all the goals associated with facilities management can seem overwhelming, it doesn’t have to be. We spoke with Cristee Monahan, VP for Central Operations at City, about which strategic objectives facilities leaders need to focus on and how to set actionable goals to meet them. Keep reading for her insights and recommendations.
Why are facilities management goals important?
The primary goal of facilities management is to ensure efficient, sustainable operations of physical spaces and assets in order to support an organization’s objectives and the well-being of occupants.
The tasks of facilities management fall under three categories:
- Supervising maintenance tasks to maximize uptime and operational efficiency
- Implementing safety protocols, compliance measures, and emergency preparedness processes
- Improving energy efficiency and sustainability practices in aligning with current standards and regulations
On the global stage, food retailers have been identified as one of the most important sectors for decarbonization. Now more than ever, facilities leaders in the industry must find ways to decrease the environmental impact of their operations in addition to their other responsibilities. Creating a more sustainable future can be regarded as both a challenge for thinly stretched managers as well as an opportunity for facilities teams who wish to be agents of change.
Setting goals is the first step for facilities managers to accomplish the tasks above while ensuring a greener future for their communities and the planet as a whole.
Even if you’ve already set facilities management goals and objectives for the year, it never hurts to stop and review them to ensure they lead to successful outcomes this year and in the years to come.
Facilities Management Goals and Objectives
The food retail industry is in an era of unprecedented change. To keep up with evolving trends, facilities managers juggle numerous responsibilities, from ensuring safety and optimizing equipment uptime to reducing energy consumption and complying with new climate regulations — all while keeping an eye on the bottom line.
Here are five key facilities management goals and objectives for FM leaders to stress in their planning.
- Improve safety, compliance, and emergency preparedness
- Increase energy efficiency and sustainability
- Stay within budget
- Maximize uptime
- Implement a proactive approach to maintenance
1. Improve safety, compliance, and emergency preparedness
Safety is fundamental to facilities management in food retail operations, where risks such as slips and falls and food-related emergencies abound.
To address potential hazards effectively, it’s critical for retailers to prioritize safety, compliance, and emergency preparedness. This begins with conducting thorough assessments in order to identify risks including refrigeration condensation, crowded aisles, and food equipment issues, as well as evaluating response capabilities for weather-related events and other emergencies.
Establishing robust safety protocols is essential for mitigating risks and ensuring swift response in case of any issues. To achieve the goal of a safety-first culture, James Halaszynski, Director of Health & Safety for City Facilities Management, recommends combining safety checklists with regular safety walks, remote refrigeration monitoring, preventive maintenance, and employee training.
“One of the most important, and costly, safety concerns is preventing slips and falls,” says Cristee. “In goal setting, facilities managers should plan for regular safety checks, including daily walks, to inspect stores.”
In goal setting, facilities managers should plan for regular safety checks, including daily walks, to inspect stores.Cristee Monahan, VP of Central Operations at City
Additionally, providing Personal Protective Equipment (PPE) such as gloves and masks as well as essential safety equipment like eye wash stations and hand sanitizer stations are important components of a safety program.
Of course, legal compliance is critical and should always be a top goal for facilities management leaders.
“Facilities managers should make it a priority to stay informed of compliance updates,” Cristee advises. “Subscribe to regulatory updates, attend workshops, and join professional organizations to ensure you’re up to date.”
Set goals for regular inspections and audits to identify areas of non-compliance, implement corrective actions, conduct employee training programs, and establish robust documentation processes to demonstrate adherence to regulations and standards.
2. Increase energy efficiency and sustainability
Given the energy-intensive nature of their operations — involving heavy-duty refrigeration, lighting, and HVAC systems — as well as their integral role in the HFC problem, grocery stores and other food retailers are pivotal players in the fight against climate change. (The average supermarket leaks 25% of its thousands of pounds of refrigerant, amounting to 70 million metric tons of C02 equivalent emissions, each year. The average U.S. supermarket also uses around 50 kWh of electricity and 50 cubic feet of natural gas per square foot per year.)
Energy efficiency and sustainability are no longer future goals but require a strategic approach today to improve the environmental impact of food retail operations — as well as increase their bottom line and continued competitiveness.
Sustainable facilities management involves minimizing the environmental impact of a facility. This is achieved by such goals as:
- Upgrading to energy-efficient equipment
- Implementing energy management systems (EMS) and smart building technologies to reduce energy consumption
- Integrating clean, renewable energy sources to reduce reliance on fossil fuels
- Reducing refrigerant gas leakage from store air conditioning and refrigeration systems
- Transitioning away from greenhouse gasses such as HFCs that increase global warming
As part of a food retail energy efficiency program, Tom Mathews, SVP of Sustainability at CBES and industry expert with nearly four decades of experience in the food retailing and distribution industries, suggests recommissioning existing equipment. According to Tom, grocery stores can see payback as soon as eight months after the recommissioning. When the corrections are properly maintained, the savings can be significant. Other methods that improve energy efficiency include:
- Updating lighting systems
- Adding variable speed drives
- Heat reclamation
- Continuous remote monitoring
3. Stay within budget
For facilities management teams, effective budget management isn’t just about monitoring expenses — it requires proactive planning that aligns financial resources with operational needs, while also accounting for unexpected contingencies.
“Staying on budget begins on the frontside,” says Cristee. “If you don’t have a workable budget to start with, you won’t be able to successfully meet that budget at year’s end.”
Achieving the objective of budget adherence should begin then with creating a comprehensive budget with built-in contingency plans. Cristee recommends the following best practices for setting a budget:
- Account for aging equipment: “As assets age, they require more resources to maintain them in their current state,” Cristee says. Components can also change over time, becoming more expensive. For example, thanks to the inclusion of electrical motor boards, the price of motor boards for simple fan motors has skyrocketed about 400% in recent years.
- Align with partners: Make sure the budget includes forecasted expenses from all partners in the facilities program — from suppliers to service suppliers.
- Weigh replacement costs against energy efficiency savings: Carefully assess the condition of the assets as well as the long-term benefits in terms of cost savings, sustainability, and operational efficiency when evaluating the need for energy efficiency upgrades.
- Maintain a strong supply chain: “Accurately estimating the costs of replacement parts and equipment depends on the strength of your supply chain,” says Cristee. Establish partnerships with vendors to ensure timely access to parts, and make sure you have an understanding of how inflation and parts availability may impact costs year-over-year.
4. Maximize uptime
Keeping equipment running efficiently is core to the facilities management role. How to achieve this with all the other demands on your time and attention is not always as straightforward as one might think.
When setting goals for operational uptime, consider these five ways to boost equipment uptime and protect assets:
- Preventive maintenance planning: Systematically approach maintenance to identify and address problems before they become breakdowns.
- Outcome-based service plans for reactive maintenance: Develop clear service level agreements (SLAs) outlining expected response times and repairs costs, and partner with integrated FM providers or utilize well-trained multi-skilled technicians to optimize service performance.
- Supply chain planning: Strengthen relationships with suppliers and plan for efficient purchasing, storage, transportation, and delivery of all products.
- Implementation of best practices for equipment operation: Establish, provide training for, and enforce all guidelines for operating equipment.
- Technology-enabled monitoring and maintenance: Streamline maintenance and ensure improved equipment performance through sensor-based monitoring, CMMS (computerized maintenance management systems), and remote monitoring.
5. Implement a proactive approach to maintenance
In the fast-paced environment of grocery stores where revenue hinges on seamless operations, the importance of effective maintenance can’t be overstated.
Rather than waiting for equipment to fail and reacting to issues as they arise, food retailers are increasingly adopting a proactive approach to maintenance. At the core of this strategy is a strong preventative maintenance program — the performance of regular inspections and proactive repairs to prevent problems before they turn into costly breakdowns.
If you’re looking to drive unprecedented efficiencies and cost savings to your retail business, transitioning to a preventive model should be a top goal for facilities management teams. Consider the benefits:
- Increasing the lifespan and productivity of assets
- Minimizing equipment depreciation
- Reducing unexpected downtime and food product waste
- Increasing efficiency of facilities management workflows
- Lowering emergency maintenance costs
- Increasing employee retention and job satisfaction
- Improving customer satisfaction and loyalty
While it may seem tempting to focus solely on reactive maintenance due to resource constraints or perceived cost savings, neglecting regular preventive maintenance ultimately leads to higher downtime and repair costs as well as potential safety risks.
In addition to regular preventive maintenance checklists, facilities managers can harness technology such as sensors, predictive analytics, and CMMS (computerized maintenance management systems), as well as leverage real-time data and analytics to anticipate maintenance needs and optimize resource allocation.
However, not all facilities are a fit for preventive maintenance. For older retail facilities, instituting a proactive maintenance program may result in diminishing returns, especially if the equipment requires frequent repairs or hard-to-find and expensive replacement parts. Higher energy consumption, increased risk of failure, and reduced performance may indicate the need to replace equipment.
“Preventive maintenance only makes sense for a newer facility,” cautions Cristee. “With old buildings and equipment, you’re going to be spending all your time on reactive maintenance because you have to.”
Transitioning from a reactive to proactive approach requires alignment across the organization. “To gain acceptance, you have to pick an area and show the benefit, ideally in terms of uptime and product loss,” Christee says.
In setting goals for establishing a preventive maintenance culture, consider these six elements of a successful preventive maintenance program.
Setting and achieving goals for food retail facilities management
Setting actionable goals in writing is a vital step in organizing the priorities and activities of facilities management teams, especially when it comes to efficiency and sustainability — which are quickly becoming the leading challenges for FM leaders. By proactively addressing these goals, facilities managers in the grocery and food retail sector can not only enhance operational effectiveness and reduce costs but also contribute to a more environmentally responsible future.
At City, as part of our industry-disruptive, data-driven delivery system for grocery stores, convenience stores, and other retailers, we can help you prioritize goals and design an implementation plan founded on today’s most effective facilities management practices. Learn more about our Integrated Facilities Management services.