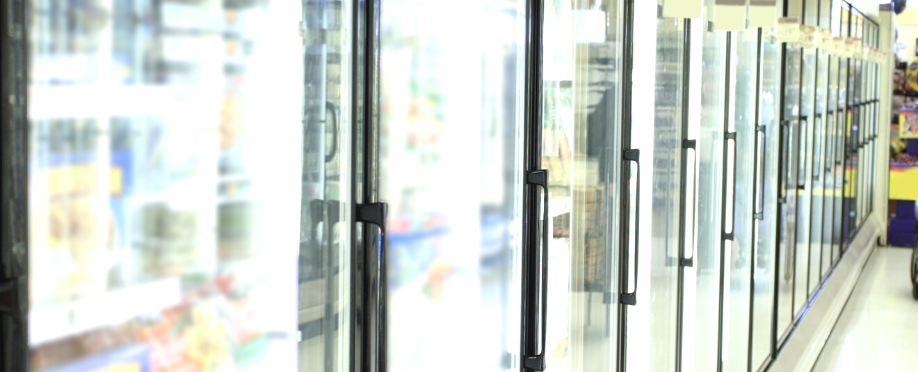
(Updated January 13, 2025)
With energy prices growing steadily and stricter sustainability standards being rolled out state after state in the U.S., grocery retailers are feeling more pressure than ever to cut back on energy consumption to both manage energy expenses and reduce greenhouse gas (“carbon”) emissions.
Fortunately, money and effort invested in food retail store energy efficiency can have a significant impact on store bottom lines — an EPA report notes that just a 10 percent reduction in energy costs for the average supermarket can increase profit margin by 16 percent.
But where do facilities leaders start? We spoke with Tom Mathews, a mechanical engineer and industry expert with nearly four decades of experience in the food retailing and distribution industries, who offered some food retail and grocery store energy efficiency tips that facilities managers can implement today. Keep reading to learn his top recommendations.
1. Recommissioning Existing Equipment
According to Tom, the lowest hanging fruit available to supermarkets today is getting the equipment you already have working efficiently. This is where recommissioning (“ReCx”) comes in.
“Whether it’s the refrigeration or HVAC system or or other facility energy-using equipment, it’s quite common to find that things ‘aren’t running quite like they’re supposed to be!’” Tom says. “Not only do we find that there are issues caused by the way the system or piece of equipment is or has been maintained and controlled, we often find there are issues that go all of the way back to when it was installed — sometimes decades back.”
ReCx, Tom explains, involves inspecting and testing all existing store energy-using systems and equipment whether located in, on, or next to the store, and restoring them to the best operating condition and efficiency that is economically practical. In other words, getting the store systems and equipment running the way they’re supposed to — sometimes for the very first time since their installation.
This may mean running as they were originally designed to run, or running as they can today in alignment with industry best practices, like using floating suction pressure control and lower minimum condensing pressure setpoints.
Energy efficiency improvements like these can come at a relatively moderate cost, from $5,000 to $15,000 depending on store size and condition and on program goals. Yet the cost savings can still be very significant: Tom estimates grocery stores can see a simple payback as soon as eight months after the recommissioning. And if the corrections are maintained, they can continue to save significantly in the long run.
Tom recommends starting with the equipment that uses the most energy and provides the highest-value functions for the store. Supermarkets will find that the energy savings and reduction of greenhouse gas emissions will make the investment well worth the effort. He also reminds facilities leaders to ensure the optimizations are maintained over time with remote, continuous monitoring of the recommissioned equipment.
Gains achieved from recommissioning often begin slipping away as soon as the ReCx technicians complete their last repair or adjustment and leave the store (or their remote commissioning workstations), Tom warns. Only permanent, continuous remote monitoring can prevent this. Tom recommends that food retailers either make remote monitoring part of their ReCx program or forgo ReCx altogether. It’s that important!
2. Updating Lighting Systems
Over the years, lighting technology has undergone a dramatic evolution in the retail industry, from inefficient fluorescents to higher-efficiency fluorescents to modern-day LED lighting. The result is that total lighting power in grocery stores has dropped from 80–100 KWH down to 20–30 KWH per month.
Nowadays, the vast majority of supermarkets have converted to LEDs. This means while in the past a lighting retrofit was the go-to solution for energy savings with the quickest returns, not to mention generously incentivized by utilities and the government, there’s now far less room for savings when it comes to lighting updates.
“In cases where grocery stores haven’t undergone LED retrofits, upgrading lighting will be important,” Tom says. “At the moment, however, there isn’t much room for improvement in lighting system energy efficiency for stores that have already converted to LED lighting.”
3. Adding Variable Speed Drives
Adding variable speed control to condenser fans, HVAC unit air supply fans, and compressor room exhaust fans — essentially any piece of equipment within the facility that moves air with a fan — can generate significant savings at a very modest cost, Tom says. After lighting, retrofits of variable speed control to HVAC unit supply fans using electronic variable speed/frequency drives (“VSDs” or “VFDs”) are the best (shortest) payback energy efficiency retrofit available to any retail store operator, whether food retailer or any other.
VSDs allow fans (or pumps) to operate at lower speeds when less air (or water) needs to be moved. “As fan speeds are reduced, the amount of air which is moved decreases on a 1-to-1 basis with the reduction in speed, but the amount of energy reduces at a rate approaching 3 to 1,” Tom explains. “So a 50 percent decrease in fan speed results in up to an 87 percent reduction in energy use, which can add up to big savings.”
In addition, slowing fan and pump speeds during utility and grid demand reduction (“DR”) calls is an easy way to deliver kW reductions to the grid and earn utility and grid DR incentive payments for your stores. This retrofit type, variable speed control, also applies to:
- Condenser fans
- Hood exhaust fans
- Motor room exhaust fans
- (In larger buildings with more complex HVAC systems) Main HVAC system return air and exhaust air fans
As a testament to the value of this technology, most new conventional HVAC rooftop units now come with variable speed control and most states no longer allow the installation of new condensers without variable speed motors.
These types of retrofits have become more common since their initial application in the late 1980s. They’re also less expensive and more reliable. Tom has one bit of advice though for any VFD retrofit: put the drive close to the motor. This is the best way to avoid a variety of motor issues that can occur. Also, avoid providing a manual or automatic drive bypass, as this will only encourage the disabling of the VFD and loss of savings.
Once installed, VFDs or any other energy retrofit equipment need to be considered part of the “serviceable system” — that is, serviced and repaired as needed, not abandoned.
An electrical, refrigeration, or energy services contractor well-versed in energy management can help add variable speed control functionality to existing equipment. “It’s a popular update and relatively easy when performed by a skilled technician,” Tom says. CBES has installed more than 10,000 VSDs on condenser and supply air fans in supermarkets all along the East Coast.
As much as VSD installations can reduce energy consumption, Tom emphasizes the importance of making these upgrades after or in parallel with recommissioning as well as implementing a system of ongoing energy monitoring. “Get the savings and other benefits, then defend the savings and other benefits,” he advises.
4. Heat Reclamation
Another huge opportunity for energy savings and decarbonization lies in the technology of heat reclamation. Supermarkets can repurpose waste heat, primarily from their refrigeration system, as an energy source in place of natural gas, propane, and other carbon-containing fuels for operations such as:
- Space heating the store
- Heating water for food processing
- Sanitation
- Sidewalk de-icing
- And more
When it comes to space heating supermarket retail spaces with refrigeration heat reclaim, Tom explains, “Think of the refrigeration systems as a really, really big heat pump that’s in place to take heat out of refrigerated cases and reject it to the outdoor ambient air via the refrigeration condensers.”
When reclaimed for space heating, the refrigeration heat is redirected to the store’s HVAC system, or systems, instead of the rooftop refrigeration condensers. At times of extreme cold and store space heating load, more heat can be extracted from the refrigeration heat pump system as required.
“You’re essentially making existing refrigeration systems work harder during these periods, so you can get more space heating out of them,” Tom says. “This causes the systems to use more electricity. But instead of using gas or propane for heating and generating more GHG emissions, you instead are using clean electricity from solar, wind, and hydroelectric power to heat your stores — heat that would otherwise be just ‘dumped’ into the outdoor ambient.”
While eliminating refrigerant leaks and replacing refrigerants with environmentally friendly alternatives is all the rage right now, Tom believes that once the issue of replacement refrigerants is addressed and gas conversions begin to roll out in an orderly multi-year process, heat reclamation will become front and center.
“It’s going to be the centerpiece of greenhouse gas reduction at every supermarket in the country,” he predicts.
[Heat reclaim] is going to be the centerpiece of greenhouse gas reduction at every supermarket in the country.Tom Mathews, SVP of Sustainability and Energy Services at CBES
5. Real-Time, Continuous Energy Monitoring
Energy monitoring has already been touched on above, but it’s worth addressing it as a separate point due to its potential impact on energy efficiency.
It’s been shown that even in food retail chains with well-managed facility management departments and processes, energy can drift by 2 percent year over year without an ongoing central remote monitoring system. By continuously monitoring the operation of a facility’s energy-consuming systems and equipment in close-to-real-time, facilities managers can not only optimize electricity usage but also respond quickly and effectively to any equipment issues before they become emergencies, even as they reduce GHG emissions by reducing energy usage and refrigerant leaks.
“Existing energy management systems already provide constant feedback on system operation and in some instances, energy usage,” Tom says. “This is vital information for facilities managers. The hard part is capturing, scrubbing, and analyzing that data and getting useful guidance from it. This requires smart people, systems, and algorithms, all working together to manage this complex task.”
One example is the SPARK+ power monitoring system, designed to continuously monitor the energy usage of refrigeration, HVAC, and other energy using store systems and equipment. Any energy performance deviation events detected are automatically dispatched for rapid resolution, ensuring wasted energy consumption is kept at a minimum.
Other approaches include CBES’ CCx (continuous commissioning) monitoring software and system and Axion Cloud’s software, which relies on pressure, temperature, and other operating information from store building, refrigeration, and equipment control systems rather than energy metering to detect and attack performance deviation events and their potential consequences. The impact of monitoring alone is such that customers can easily achieve reductions in energy use, or more correctly, avoid energy usage by 5 percent with the best monitoring services achieving much more.
6. Other Energy-Saving Tips
The tips above are a great place to start and can all result in significant energy savings and emission reductions. However, there are many, many other measures that can be taken, including:
- Eliminating refrigerant leaks: An important sustainable refrigeration practice, an effective leak reduction program can achieve not just refrigerant savings and direct GHG emissions reductions, but significant energy savings and indirect GHG emissions reductions as well. This is because undercharged refrigeration systems, almost the norm in many U.S. supermarkets, run less efficiently and use more energy as a result. The reasons are complex but the efficiency loss has been confirmed by government-sponsored field tests. If you’re managing refrigerant losses by minimizing refrigerant charge, make sure the minimization of charge does not end up maximizing your refrigeration system’s energy usage.
- Using efficient, low-GWP refrigerants: Grocery stores that still use CFC refrigerants such as R-22 should replace them with HFCOs, or even more environmentally friendly options like HFO blends, which are zero ODP (Ozone Depleting Potential) as well as low-GWP (Global Warming Potential) gases. In many instances, these replacement refrigerants can offer a refrigeration system energy efficiency bump as well. Careful research of candidate refrigerant properties and performance and engineering reviews of existing refrigeration system designs and operating characteristics will be required, however.
- Optimizing refrigeration cases: “Closing the case” is fast becoming a mantra in the world of supermarket refrigeration energy savings. As food retailers’ historical resistance to glass doors on refrigerated cases drops in the face of rising concern among their customers about sustainability, the doors to great energy savings (and other benefits as well) are thrown open. Retrofitting glass doors on open refrigerated cases is the number three ECM (energy conservation measure) to be applied, after (number one) LED lighting and (number two) supply fan VFDs. Novel case architectures, signage, lighting, and other measures can help merchandisers get more comfortable so that they can still work their magic with clients even with a layer of glass between the client and the food products.
- Anticondensate Heater Controllers (ACHCs): Electronics that control the amount of power that flows into glass door heaters have been around since the 1980s but not in the form they’re in today — effective, reliable, able to communicate, and “smart.” Make this your ECM number four and stop delaying. Cold cases with glass doors will always require heat to keep the glass clear. Better to have doors that are built with enough heat to always be able to “clear” even when store humidity is not properly controlled, and then use ACHC to minimize actual ACH energy use when humidity is low and properly controlled. “Nothing maddens food retail merchandisers and operating VPs more than clouded glass doors. If you want them to love glass doors and all the benefits they provide, then make sure they’re always clear and easy to see through,” Tom says. “ACHC your way to acceptance and low energy usage.”
Sustainable Energy Solutions for the Future of Retail
In today’s global environment, it’s more important than ever for supermarkets and other retailers to do their part in reducing energy consumption and greenhouse gas emissions. By following the tips above, retailers can have a significant impact on their facilities as well as on the planet.
CBES is passionate about helping facilities management programs and managers conserve energy and reduce emissions.