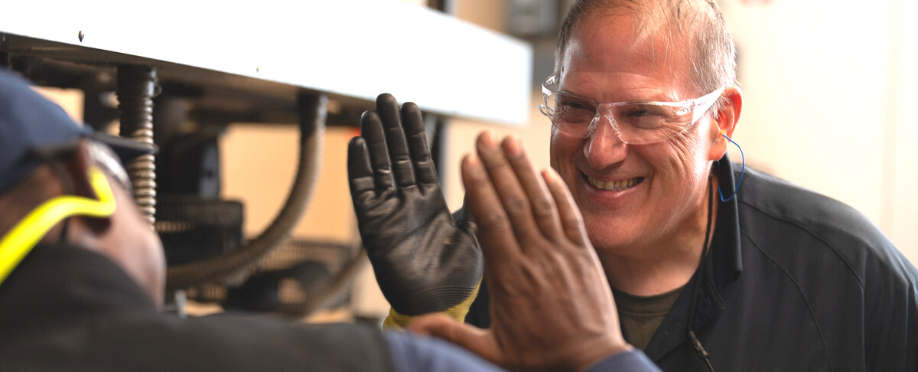
Implementing a preventive maintenance model is one of the most effective ways to save on maintenance costs, extend the life of equipment, and boost employee satisfaction and retention — making it critical for any facilities management initiative. As preventive maintenance checklists are at the center of any successful planned preventive maintenance (PPM) program, learning how to strategically create and utilize them is key.
“Preventive maintenance is a never-ending job for a facility manager, but at the same time, high-quality PPMs make facilities managers’ jobs a lot easier,” says George Campbell, who as Director of Technical Services at City oversees service delivery to grocers and other retail clients. “As I like to say, ‘Major PPMs bring major returns.’”
Major PPMs bring major returns.George Campbell, Director of Technical Services at City
As part of daily operations, his team employs dozens of preventive maintenance tasking sheets with notable outcomes all throughout the year. Keep reading to learn some of his top best practices.
Must-Have Planned Preventive Maintenance Checklists
When asked which preventive maintenance checklists are most important out of the dozens he employs on a regular basis, George answered, “All of them,” but we managed to have him narrow down the priority lists as follows. Most facilities management teams have specialized PPM crews that implement such checklists on a quarterly or biannual basis, or annually at the very least.
Building Envelope
- Frequency: Annual inspection with generated work orders for wear items and repairs
- Recommend checklists:
- Structure
- Interior/exterior
- Grounds
Refrigeration
“Refrigeration is one of the most important pieces of a solid PPM program, as it is the biggest source of shrink,” George says. “If you don’t maintain the refrigeration, it will start failing. What would happen if you drove your car without changing the oil? Refrigeration equipment is no different.”
- Frequency: Annual inspection with generated work orders for wear items and repairs
- Recommended checklists:
- Racks and compressors (priority)
- Condensers and evaporators (priority)
- WIC/F (Walk-in coolers and freezers)
- Cases and self-contained refrigerant systems
HVAC
- Frequency: Annual inspection with generated work orders for wear items and repairs
- Recommended checklists:
- Spring (cooling system) and fall (heating system) at a minimum
- RTUs/Splits (roof top units/AC split systems)
- AHUs (air handling units)
- Exhaust fans
Electrical
While facilities are often reluctant to allocate funds for electrical PPMs, power outages can be quite costly. Annual preventive maintenance can prevent a catastrophic failure, and downtime costs more than inspection time, George points out.
- Frequency: Annual inspection
- Recommended checklists:
- High and low voltage EDCs (Electrical Distribution Centers)
- Infrared scanning for all distribution panels
- Major equipment (e.g., compactors, balers, cranes)
Plumbing
- Frequency: Annual inspection
- Recommended checklists:
- Backflow prevention inspection (compliance)
- Sewer jetting
- Hot water heaters
Facilities Preventive Maintenance Checklists: Best Practices
And how do you ensure it gets executed properly? By implementing the following best practices, you can ensure your preventive maintenance checklists contribute to the overall efficiency, safety, and longevity of equipment in the food retail facilities sector.
Start with critical equipment and systems
Prioritize essential equipment for food safety, compliance, and facility functionality, which in grocery stores and other food retail facilities typically encompasses refrigeration systems, HVAC, cooking equipment, and lighting.
Consult manufacturer guidelines
Refer to equipment manuals and manufacturer guidelines to establish recommended maintenance schedules and procedures. Integrate these guidelines into your checklist for each specific piece of equipment.
Adjust maintenance schedules appropriately
Consult manufacture guidelines and account for environmental conditions impacting equipment performance, such as summertime’s high temperature and humidity, when determining maintenance schedules. Indicate the schedule on checklists — daily, monthly, quarterly, biannually, or annually — accordingly.
Include safety guidelines
Safety should be paramount — include checklist items that ensure all assets operate safely and address potential hazards related to gas leaks, electrical issues, and more.
Prioritize energy efficiency
PM checklists are a great opportunity to not only reduce maintenance and asset replacement costs, but by aligning them with sustainability objectives, they can further reduce operating costs by lowering energy consumption.
Include tasks promoting energy efficiency, such as the following, for a positive impact on your energy bill as well as the environment:
- Refrigeration systems: Check condenser coils, check and replace door gaskets, and monitor and calibrate thermostat settings.
- HVAC systems: Change air filters and inspect and clean HVAC ducts.
- Lighting: Upgrade to energy-efficient LED lighting where applicable.
- Cooking equipment: Clean and maintain exhaust hoods and ensure proper calibration.
- Insulation and seals: Inspect doors and windows for air leaks, and check insulation in refrigeration units.
- Energy Management Systems (EMS): Regularly update and optimize settings and ensure staff are well-trained on proper EMS controls.
- Water heating systems: Inspect and maintain for efficiency.
- Electrical systems: Inspect for energy wastage.
Clearly define document inspection criteria
Clearly define acceptable performance levels, visual indicators, and measurements, and provide detailed instructions for technicians during inspections.
Keep good records
Implement an efficient and organized record-keeping system to track maintenance activities, inspections, and repairs, and ensure technicians are well-trained in them. Issues discovered during inspections and the corresponding actions taken should be documented.
Implement a robust training program
It’s not a coincidence that as City’s Director of Technical Service George is the company’s number-one proponent of technician training. Not only do facilities managers need to ensure staff are adequately trained on preventive maintenance checklist procedures, but it’s also imperative to provide them with ongoing training to help them grow their knowledge and keep them updated on industry best practices. At City, we go a step further by cross-training technicians in multiple disciplines. To learn more about the technician training program George oversees, check out our Facilities Management Training Tips.
Regularly review and update checklists
Facilities environments are always in flux. Periodically review and update PM checklists to incorporate changes in equipment, regulations, or industry best practices. Use feedback from technicians and equipment operators to enhance effectiveness.
Facilities Preventive Maintenance Checklist Example
George provided us with an example of one of his tried-and-true PPM tasking lists for one the most critical systems in food retail facilities — refrigeration. See below and right click to save for future reference.
A Proactive Approach to Facilities Management
Making the shift from reactive to preventive maintenance can seem daunting for facilities teams, but the effort will more than pay off in terms of managing costs, maintaining job satisfaction, and increasing asset uptime. As part of this transition, preventive maintenance checklists are sure to serve as an invaluable tool.
At City, we offer an industry-disruptive delivery system for facilities management founded on preventive maintenance that significantly delivers exceptional service and sustained cost savings. Learn more about our integrated facilities management services.