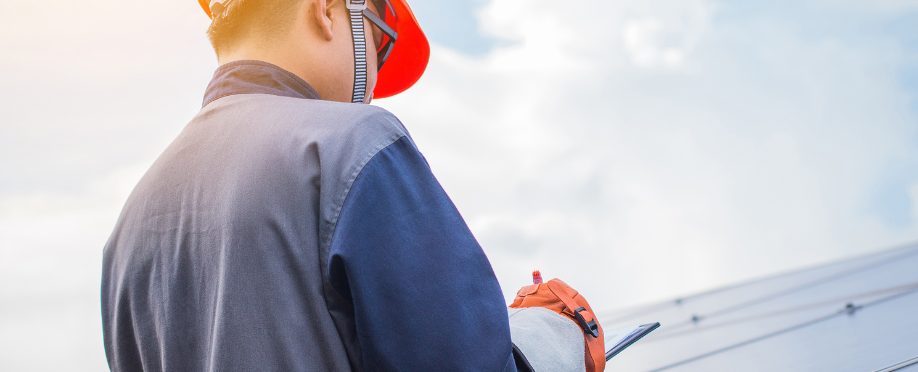
One of the biggest opportunities in the facilities management field today is without a doubt making the shift to a preventive maintenance model. Not only does an effective planned preventive maintenance program (or PM program, for short) result in significant savings in emergency maintenance repairs, but it also extends the life of equipment and boosts employee retention.
As the Director of Technical Services at City, George Campbell oversees service delivery to grocery store and other retail clients. One of the most critical parts of his job is designing and implementing PM programs. Keep reading to learn the elements of preventive maintenance as well as the best practices George lives by for a successful preventive maintenance program.
What Is a Preventive Maintenance Program?
A preventive maintenance program, otherwise known as a preventative maintenance program, is a maintenance approach involving regularly servicing assets to prevent unexpected breakdowns, increase uptime, and extend asset lifespan.
What is planned preventive maintenance?
Planned preventive maintenance is a key part of any planned preventive maintenance program and refers to the activity of scheduling and carrying out planned maintenance tasks in order to prevent equipment failure. Such tasks are carried out in advance based on factors such as time, usage, or condition, rather than facilities managers waiting for equipment to break down.
“The PM program is the overall strategy, and planned preventive maintenance is how that strategy gets implemented,” George explains.
The PM program is the overall strategy, and planned preventive maintenance is how that strategy gets implemented.George Campbell, Director of Technical Services
There can be said to be four types of preventive maintenance:
- Time-based maintenance, which is performed at regular time intervals (e.g., monthly or quarterly inspections)
- Usage-based maintenance, which is triggered by equipment usage (e.g., every X,XXX operating hours)
- Predictive maintenance, which is based on real-time data and condition monitoring, alerting teams to potential issues before failures occur (e.g., using sensors to detect vibration or temperature changes)
- Prescriptive maintenance, which uses AI and advanced analytics to not only predict failures but also recommend the best course of action to prevent them
6 Steps to an Effective Preventive Maintenance Program
Ready to start a PM program or looking to refine your current approach? George recommends the following steps for making planned preventive maintenance a cornerstone of your organization’s facilities management strategy.
1. Build a Proactive Culture
The biggest source of failure when it comes to a preventive maintenance program is failing to fully commit to one in the first place. This makes getting buy-in for a proactive approach one of the most important steps for ensuring success. As George explains, preventive maintenance must be embraced as the foundation of your facilities management program, or you simply won’t make time for it.
“The retail industry is still rife with companies who prefer a reactive model of business to the detriment of their bottom line and their employees’ well-being,” George says, who knows from experience — four decades in the business as a master electrician, HVAC technician, refrigeration technician, and EMS controls specialist — the value of proper preventive maintenance. “But if you do good, solid PMs, reactive work orders slow down, your equipment lasts longer, you get fewer breakdowns, and there’s less weekend work.”
Take the time to work with leadership and key personnel to ensure they’re on board with a policy of preventive maintenance, the benefits of which include:
- Increased lifespan and productivity of assets
- Minimized equipment depreciation
- Reduction of unexpected downtime and food product waste
- Increased efficiency of facilities management workflows
- Lower emergency maintenance costs
- Enhanced work-life balance with fewer overtime and weekend hours
- Higher employee retention
- Higher customer satisfaction and loyalty
2. Establish goals and track KPIs
The success of a PM program depends on its results, which makes setting clear goals and tracking key performance indicators essential for optimizing an organization’s facilities operations.
“If you’re not measuring what you’re doing, you have no way of proving your PM program is saving money and reducing downtime,” George says.
Start by aligning your preventive maintenance goals with strategic business priorities. Such objectives may include reducing reactive maintenance costs, extending equipment lifespan, improving technician efficiency, or enhancing the customer experience.
Once goals are set, measure success with maintenance KPIs that provide actionable insights into the program’s effectiveness, such as planned maintenance percentage (PMP), which compares time spent on planned vs. unplanned maintenance, and mean time to repair (MTTP), which the average time required to diagnose, repair, and restore a failed asset to full functionality.
With a robust tracking system in place, in particular through a CMMS or an enterprise solution like Microsoft Dynamics 365, which City uses to manage service workflows and optimize operations — facilities managers can analyze trends, adjust preventive maintenance schedules, and refine strategies over time to ensure goals are met.
3. Develop a comprehensive planned preventive maintenance plan
Of course, you can’t have a successful PM program without solid preventative maintenance plans. An effective preventive maintenance plan includes the following elements:
Asset inventory
Inventory should include make, model, serial number, specifications and capabilities, location, acquisition date, expected lifespan, and QR or barcode for identification and tracking.
Asset maintenance history
Track dates performed, parts used, labor and parts costs, and current condition.
Tasking sheets
The tasking of a PM plan consists of two types of recommendations, which can be derived from the owner’s manual for any piece of equipment.
- Owner- or user-scheduled maintenance: This would consist of regular checking, cleaning, and adjustments performed by users of the equipment.
- Service provider scheduled maintenance: These are the maintenance activities performed by skilled tradesmen on a regular basis.
Over the years, George has accumulated his own tried-and-true best practices, which he adds to his tasking sheets. Nowadays digital formats allow technicians to access tasks via smartphone or tablet.
Additionally, facilities managers should provide best practices for handling equipment by its daily operators. Basics such as regular cleaning and proper handling can go a long way to prevent excessive wear and tear, avoid breakdowns, and extend the life of store equipment.
Inspection
Regular inspections in accordance with preventive maintenance checklists should be part of a PM plan to ensure the equipment is running properly and safe to operate.
Prioritization
Maintenance scheduling should be guided by how important the asset is to daily operations, giving high priority to safety concerns. For example, air conditioning, refrigeration of perishables, front doors, and generators during storm season would be high priorities for grocery and convenience stores.
Schedule
Preventive maintenance should be scheduled to minimize disruption to operations and customer service based on time periods (by month, quarter, etc.) or usage, such as hours of operation. In addition to establishing fixed schedules, facilities teams can set up automated triggers for when specific performance thresholds are met, based on metrics like runtime hours, sensor alerts, or equipment performance thresholds. This ties maintenance tasks not just to the calendar but to real-world wear and tear.
4. Train technicians for long-term success
Given the intimate connection between service quality and the effectiveness of a preventive maintenance program, George also runs City’s technician training programs. It also happens to be his favorite part of his job. “My passion is seeing the lightbulb turn on in the technician when they have that ‘aha’ moment,” he says.
With the central role that customer experience plays in today’s retail industry, service quality and speed have never been more important. At the same time, there’s a critical shortage of technicians across the trades. Without enough people to do the work, George explains, there’s a lot more demanded of today’s technicians. Not to mention, young tradesmen coming out of school don’t have the experience needed to keep up.
The burden falls on facilities management leaders to ensure their technicians are well-trained — and ideally, in multiple trades as multiskilled technicians. For example, at City, multi-skilled technicians solve 90 percent of FM issues with lower costs and faster fixes.
George’s secret is coupling a robust self-study program with a hands-on training program. For a one-of-a-kind experience, technicians get to practice at a training center stocked with the same equipment they’ll be using for City’s partners in the field. “We set it up like a retail/grocery store so that it’s 100 percent operational,” George says. “You could cook chickens and bake bread if you wanted to.” To simulate real-world conditions, the instructors sabotage the machines and the technicians bring them back into working order.
The program requires a lot of discipline, George says, but it’s well worth the effort. His technicians are fully prepared to not only handle any and all reactive maintenance needs, but they’re also, thanks to cutting-edge predictive technology, well-equipped to execute an effective preventive maintenance program.
5. Incorporate predictive maintenance
All too often, the critical step of prediction is left out of PM programs, but George considers it to be the foundation of any successful FM strategy — not to mention, the future of maintenance.
Today there are a number of different predictive maintenance technologies, including ultrasound technology, vibration analysis, infrared analysis, laser-shaft alignment, oil analysis, and predictive analytics using AI and machine learning. George uses SOUNDTech+ powered by DST, the City branded predictive maintenance ultrasound tool, which according to field experience can predict catastrophic refrigeration and HVAC compressor and rack failure before it becomes an issue with up to 98% accuracy.
Predictive maintenance goes a step further than preventive maintenance, allowing for more informed decision-making and capital planning. It also provides more precise diagnostics for technicians, saves time in the field, and prevents breakdowns before they result in unexpected downtime, product loss, and emergency maintenance calls.
6. Implement regular corrective actions
Corrective maintenance is a term that is sometimes used synonymously with preventive maintenance, but it technically refers to maintenance tasks and repairs designed to restore equipment to proper operating condition.
In the grocery industry, retailers commonly recommission equipment every two to three years in order to correct issues and restore efficiency. “The beauty of predictive technology is it allows you to take steps today to keep equipment in good working order, instead of letting issues build up over time,” George says. “This means you don’t have to do recommissioning as often or at all.”
The beauty of predictive technology is it allows you to take steps today to keep equipment in good working order, instead of letting issues build up over time.George Campbell, Director of Technical Services
Even with recommissioning, you’ll lose efficiency with equipment over time, but the decline doesn’t have to be so fast. With regular correction, powered by a reliable predictive technology tool, you can stay as close to optimal efficiency as possible.
7. Forecast capital asset needs
Finally, the last element of a solid preventive maintenance program is capital asset forecasting, which ensures a solid capital program. While the steps above will ensure you’re getting the most out of your equipment, nothing lasts forever and over time assets break down. With proper forecasting, you can understand when to repair and when to replace equipment and ensure you have the funds in place as needed.
Read more: |
A Proactive Approach to Facilities Management
Gaining the competitive edge is critical in today’s retail industry. And with unprecedented inflation, rising energy costs, and a shrinking skilled labor pool, managing FM costs and maintaining employee satisfaction will play a significant role in determining success.
At City, we offer an industry-disruptive delivery system for facilities management founded on preventive maintenance that can help your business get ahead. Learn more about our Integrated Facilities Management services.