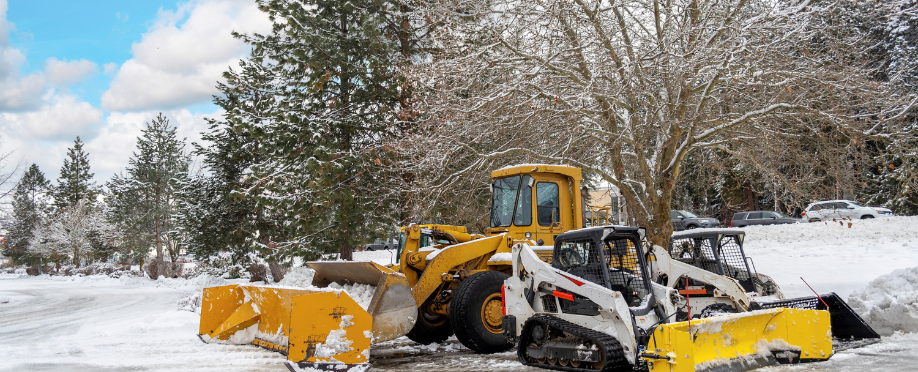
Just as with anything in facilities management, when it comes to mitigating the impact of the winter season, taking a preventative approach is always the best — allowing facilities managers to avoid issues before they lead to costly repairs, customer issues, lost product, and threats to personal safety.
We spoke with Brendan McGael, Snow Manager for City US and seasoned winter weather veteran, who’s been braving low temperatures and hard winter conditions himself for decades. He recommended some helpful steps and insider tips for helping facilities managers brace themselves for the winter season. Keep reading for an in-depth winter checklist that will help retail stores prepare for, and hopefully avoid, some of the most common wintertime facilities management issues.
Winter Checklist: 8 Steps to Get Your Retail Facilities Ready
1. Repair damage to concrete
Your first steps in preparing for the winter will happen well ahead of the season, Brendan says. Repairing concrete is one of the most important off-season maintenance items to check off your list — ideally in the springtime — before concrete structures become susceptible to the freeze-thaw effect. This will help prevent damage to snowplow equipment come wintertime as well as interior and exterior facilities damage that could result in structural instability.
2. Tackle your winter maintenance checklist
Winter’s extreme conditions can take a toll on facility assets, but a winter maintenance checklist can go a long way in detecting and preventing issues before they lead to asset downtime, equipment failure, and safety risks. In the fall, well before winter conditions arrive, facilities managers should run through this list and take care of any issues that come up.
Make sure your winter maintenance checklist items include:
- Check facilities for drafts or cracks in the structure
- Make sure doors and windows are weatherproof
- Inspect the HVAC system and replace the filter
- Inspect plumbing for signs of excessive moisture and seal cracks and openings around exposed pipes to prevent freezing
- Clear gutters and inspect the roof for signs of damage
- Ensure adequate backup generators and other emergency equipment are on-site and ready in case of power outages
- Cut off the water supply to sprinkler systems and hoses around the property, and drain the pipes in the Garden Center
- Inspect trees and power lines around the property for potential risks
- Designate a dedicated area for piling snow safely away from cars and pedestrians
- Check exterior lighting and replace bulbs if needed
3. Revisit your winter disaster preparedness plan
Facilities management leaders should revisit their winter disaster preparedness plan every year, the earlier the better. Brendan recommends finalizing this critical document in the fall: “Mother nature comes when she wants to. We’ve already had two events this year, and it’s only October. Those first ones always seem to catch you off guard.” Ensure the appropriate personnel or your external vendor monitors conditions on a daily basis and sends regular weather reports. Weather support vendors should be briefed on the disaster preparedness plan as soon as it’s approved so they’re ready to go in the case of a winter storm.
4. Establish standard operating procedures for snow clearing
Come November first, Brendan advises that Regional Facilities Managers assign responsibilities for snow cleaning and other winter maintenance procedures and establish Standard Operating Procedures (SOPs) for snowplowing vendors. Every store should have their own unique SOP for snow clearing.
After overseeing the standard operating procedures for over 700 stores in his territory for City for a number of years, Brendan has SOPs down to a science. He recommends the following best practices:
- Lay out the process explicitly. List step-by-step every action in the scope, including plowing, shoveling, salting, and hauling snow. “Make sure you don’t leave any room for ambiguity before you send an SOP to a vendor,” Brendan advises. “I’ve seen plenty of instructions missing, and this opens the door to issues.”
- Use clear and definite language regarding expectations such as “you will” or “you must.”
- Clearly state liabilities. Brendan always ensures it’s stated that the vendor is 100 percent liable for the store’s snow clearing operations.
- Get approval from your Legal department. “An SOP, after all, is a binding contract,” says Brendan.
5. Secure a good snow vendor
With your snow clearing SOP drawn up and approved by Legal, it’s time to secure a good vendor. “Taking the time to vet the vendor carefully is hands down the most important thing you can do to ensure a successful winter season,” Brendan says. As with most things in life, you often get what you pay for. “The best price isn’t necessarily the best company for the job,” he adds. “Above all, you want to make sure your vendor is reliable and can follow your exact procedure.”
Above all, you want to make sure your vendor is reliable and can follow your exact procedure.Brendan McGael, Snow Manager at City US
6. Do a walkthrough with your snow vendor
At the start of your engagement, the store manager should walk the exterior with the vendor in order to note:
- Damage to curbs, sidewalks, signs, and lights, as well as potholes, which can destroy equipment
- Where exactly snow is going to be piled
- Where your equipment is going to be stored
This can help clarify instructions and prevent potential disagreements down the road. During the walkthrough, take pictures.
7. Prepare the interior for safety
In order to ensure the safety of employees and shoppers, take all due precautions against wet floors to prevent falls. Place absorbent, slip-resistant rugs at store entrances, keep the front walk clean, dry, and ice-free, and place wet floor caution signs as needed inside the store.
8. Stock up on de-icing materials
Invest in de-icing materials and ensure they’re on-hand and easily accessible. Many people use straight rock salt, but Brendan recommends calcium chloride, which he says works better and doesn’t refreeze at below-zero temperatures. Popular storage options include using on-site portable storage containers or keeping materials on the ground contained by a brick corral or jersey barriers and covered by a tarp.